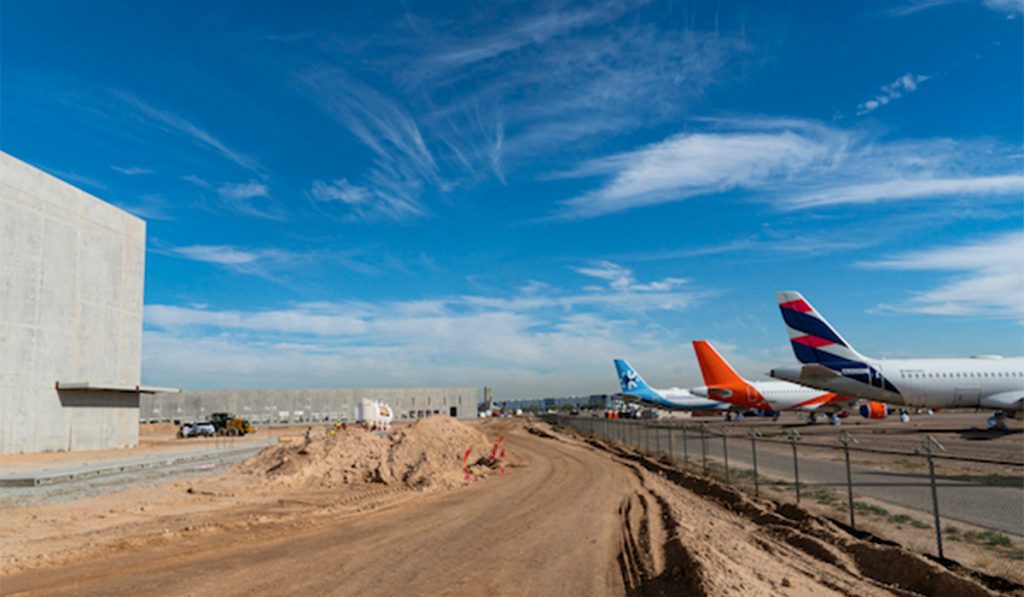
Airpark
In its fourth quarter Construction Delivery Outlook report, leading national design-build firm LGE Design Build examines key trends in construction labor, supply chain, material costs and demand to determine what will define the industry in 2023.
“Amid the speculation and uncertainty of a looming recession, this report provides critical insights that can help guide leaders within all sectors of the construction industry so they can make informed decisions for their businesses and their teams,” says David Sellers, president and CEO of LGE Design Build, which has been a leader in the Southwest’s commercial market for close to 30 years. “Demand for non-residential construction has slowed and is expected to do so into the new year. However, e-commerce sales and industrial demand in our markets has remained strong, which gives reason to be hopeful that the commercial construction sector is stable enough to withstand the otherwise bleak economic forecast.”
A summary of the Construction Delivery Outlook key findings include:
Construction Labor
The construction unemployment rate is still below pre-pandemic levels but the demand for skilled workers remains. Despite the economic challenges presented in the first half of the year, general contractors and subcontractors are still looking to fill positions. The struggle to hire contributes to rising project costs and overall delays, which are expected to continue into 2023.
From September to October 2022, the construction unemployment rate rose from 3.4% to 4.1%, which is still well below the pre-pandemic mark of 5.5%. Only 1,000 positions were filled in the construction sector in October as the skilled trades continued to struggle to fill roles that were vacated by older workers who opted for early retirement during the shutdown. In fact, approximately 1 million apprentices will be needed by 2023 to fill the vacant positions in skilled trades.
Supply Chain
Supply chain issues across water and land continue to improve, giving the construction industry cause to be optimistic into the new year. However, certain materials remain difficult to source and the long lead times put additional strain on the industry. The Los Angeles and Long Beach ports are currently seeing an average of nine ships waiting in their harbors, although this pales in comparison to the record 109 vessels at the peak of the congestion in January 2022.
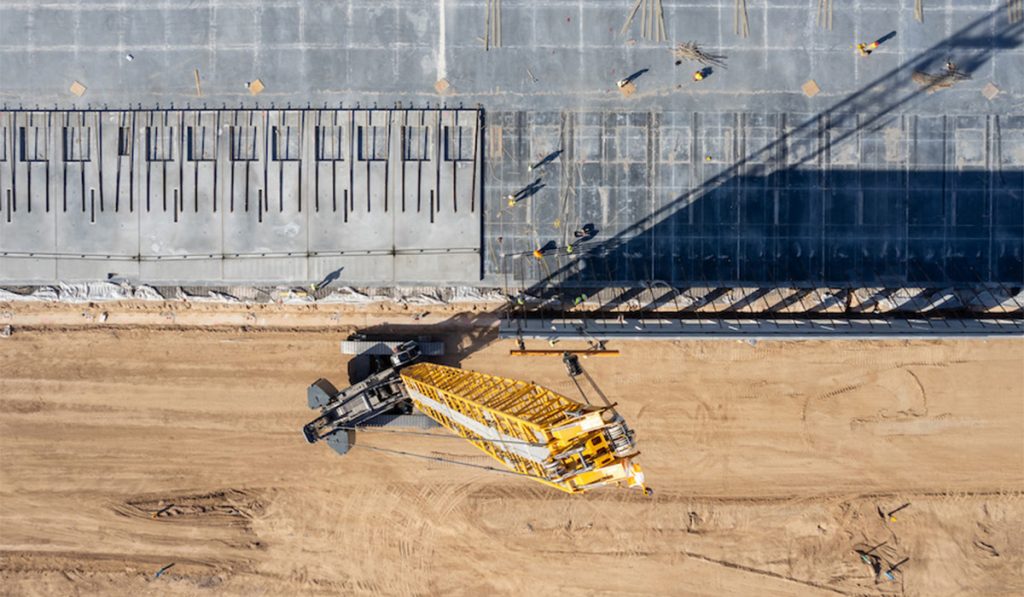
Crimson Canyon
Additionally, due to a high retirement rate that is not being offset by a younger generation entering the field, the trucking industry is still in need of 78,000 drivers. This labor shortage is consistent throughout the nation, as well as on a global scale.
Recent legislation, including the Infrastructure and Jobs Investment Act and the U.S. Maritime Administration’s Port Infrastructure Development Program, should eventually alleviate some of the remaining stress on the supply end.
Material Costs
With demand for certain sectors cooling off, many material prices continue to either stabilize or drop. While factors such as geopolitical instability, inflation and gas prices are expected to continue to add strain to the supply chain, these obstacles are not impacting material costs to the extent that they were in early 2022.
In fact, there has been a stark improvement in the cost of steel mill products and lumber since May 2022. Aside from July, when lumber leveled off, both have steadily declined in the last six months. And, while cement, concrete and flat glass prices continue to rise and copper prices remain high, the overall costs have begun to trend back downward.
Demand for Industrial Construction
The annual rate of non-residential construction dipped by 15.3% during the third quarter, reflecting the anticipated response to the Federal Reserve raising interest rates. However, demand for the industrial product type remains strong.
The rise of e-commerce sales since the beginning of the pandemic has been a key catalyst for industrial growth and e-commerce sales are expected to surpass $1 trillion this year, highlighting the lingering demand for warehouse space. In the Phoenix metro area, there is more than 46 million square feet of industrial construction taking place, making Phoenix second only to Dallas, with just shy of 67 million square feet under construction. On a national level, the industrial pipeline is at a record 689 million square feet.
Architectural teams are also facing unique obstacles caused by construction unemployment, supply chain issues and material volatility. These teams are tasked with conceptual design, preliminary pricing, entitlements, construction documents and construction administration through completion. Many of these crucial steps are experiencing long lead times caused by heavily booked due diligence consultants, ever-changing design expectations from municipality Design Review Boards, and increasing entitlement and permit review durations.
Photos courtesy of LGE Design Build